Apparel Production: Outsourcing to Owning the Process
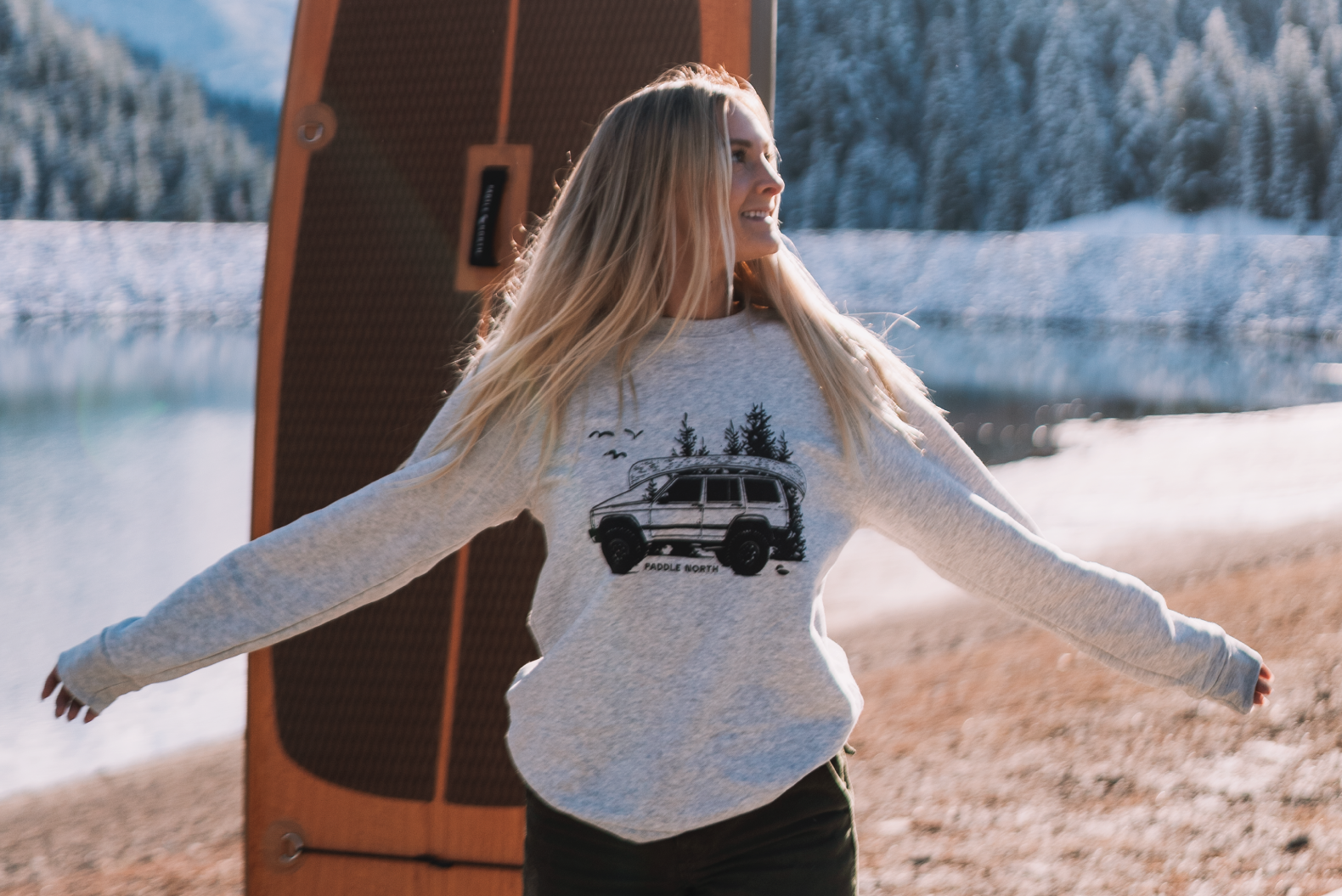
Most people know us for our hard goods-- paddle boards, kayaks, surf boards and utility docks. Did you know we also have a growing line of soft goods? For the past 10 years, we've been going through different levels of apparel development.
Level 1: Outsourcing Production and Printing on Generic Items (Bella Canvas, District, Alternative Apparel, etc.)
At this initial stage, our focus was on establishing our brand and testing the market. Outsourcing to a local screen printer allowed us to minimize upfront investments in equipment and inventory. However, the downside was lower margins due to the printer’s markup and not a lot of uniqueness in the product.
Level 2: In-House Production on Generic Items
As our volumes grew, it made financial sense to invest in our own screen printing equipment. This move cut out the middle layers, thus improving margins. The trade-off was the additional work and the need to manage the production process directly, with no improvement in product uniqueness.
Level 3: Full Product Development and Direct Factory Production
This is where we currently are.
This approach allows for maximum customization and margin improvement but requires a deep understanding of the manufacturing process, quality control, logistics, and inventory management. There are high order quantities and the risks are much greater. Tech packs (or the manufacturing prints/instructions) need to be clear.
We’re improving here and coming out with some really unique apparel items. The “soft goods” category has never been a major focus for Paddle North, but I am excited to see how far it can go.
Comments